WE ARE ALL INCREASINGLY AWARE THE IMPACT THAT PLASTICS ARE HAVING ON OUR PLANET – TAKING HUNDREDS OF YEARS TO DEGRADE AND WITH ONLY 9% OF ALL PLASTIC WASTE BEING RECYCLED TO DATE* – SO WE ARE TAKING DRASTIC ACTION TO FIND ALTERNATIVE, CLOSED LOOP SOLUTIONS FOR SINGLE USE PLASTICS.
Through switching to alternatives and prioritising low impact packaging, to date, 95% of our packaging is either recyclable, compostable or reusable. We will reach 100% by 2025.
Polybags account for nearly 10% of our total packaging weight produced every year. We buy around 40 million individual bags to protect our garments in transit - from factory to customer. They are thin, clear, and as of 2020, we made sure they contain minimum 30% recycled content.
The unique thing about this recycled content is that it is from old polybags – pioneered by Mainetti’s PolyLoop technology.

The opportunity here is polybags are typically made from LDPE – a technically recyclable type of plastic – but by not controlling the route of disposal (the end of their life) we cannot be sure that they are practically recycled; instead potentially ending up feeding incineration plants, ocean pollution or in landfill.
By partnering with Mainetti and continuing to use these polybags, we are not creating a waste, instead a closed loop resource in a circular system.
We therefore believe closing the loop is the best possible solution we have found to date.
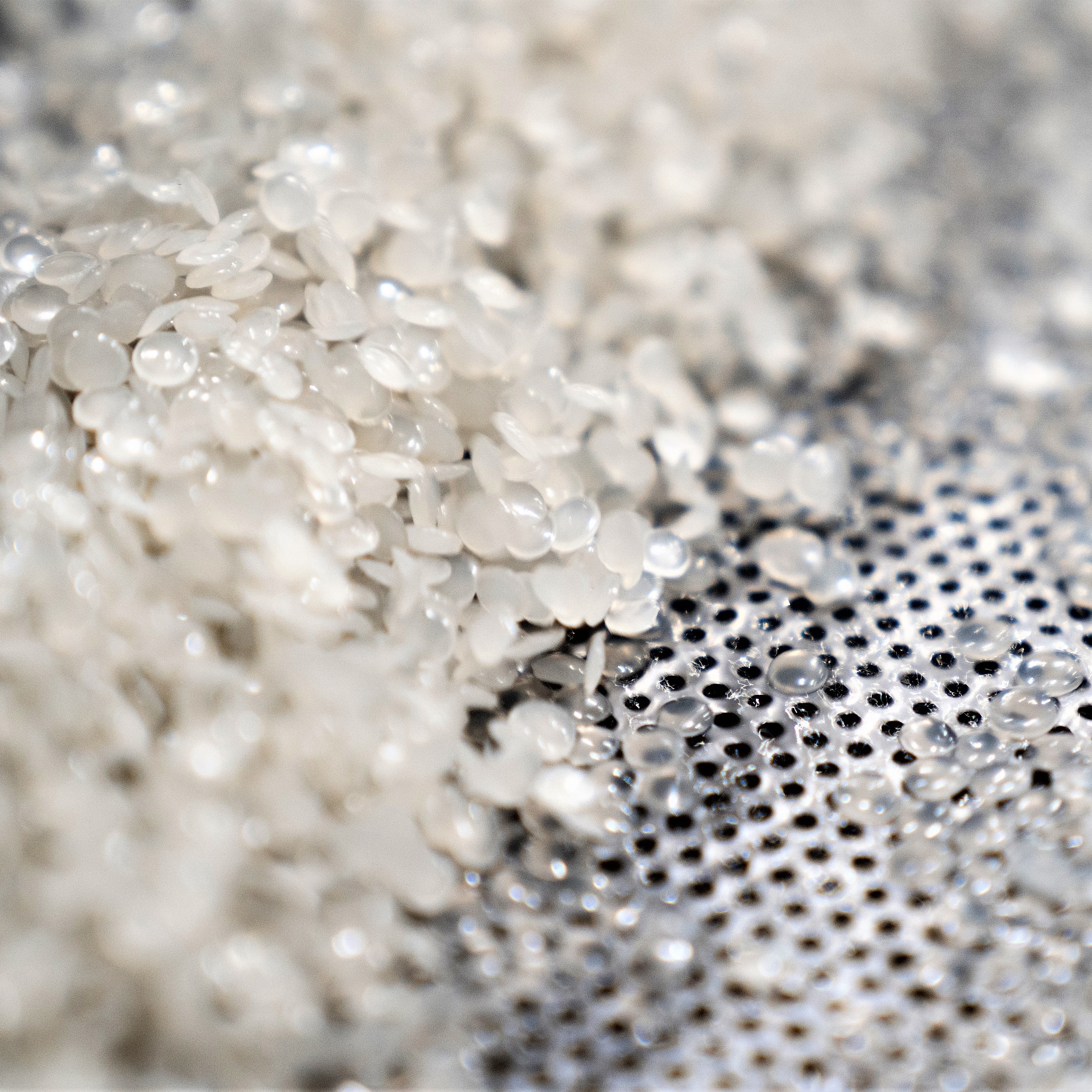
Having launched this initiative, we have found a few truths we have come across in the last year:
1. Polybags serve a function and getting rid of them could cause more harm than good.
Polybags provide essential protection when storing and transporting our garments from factories to warehouses.
Without them, we increase the risk of damage to our garments.
This in turn has a financial and environmental cost – wasting the energy, water and resources used to make each garment – which goes against our passion and beliefs to creating the highest quality garments that remain loved and worn for longer.
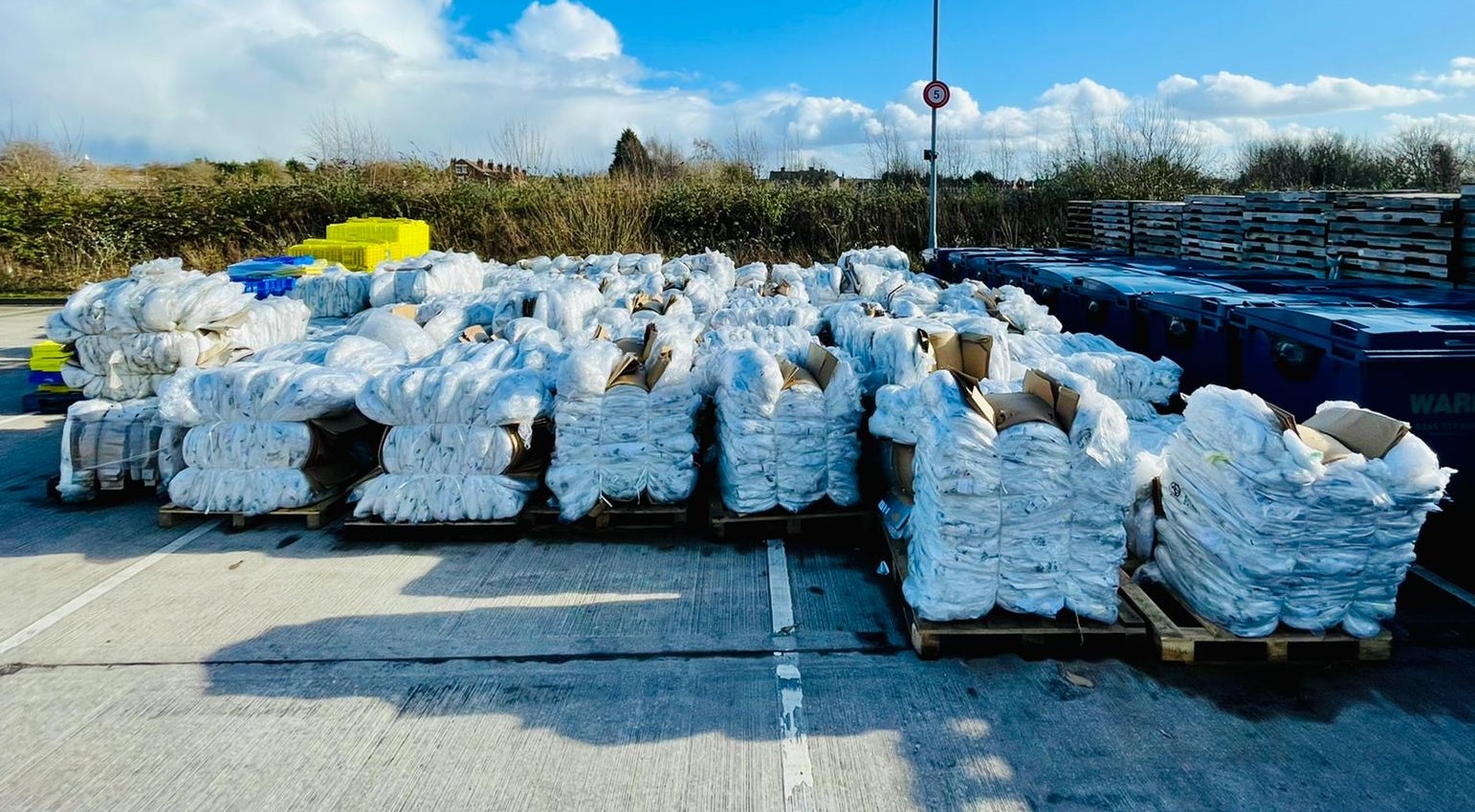
2. Polyloop helps us control where our bags end up.
We know that the poly bags we send to Mainetti’s Polyloop facility will not end up in landfill.
This is made possible by our warehouse teams that remove the bags from the product before sending it out to our stores. They then consolidate the bags and send them to Mainetti’s polyloop facility in Wrexham (90 miles away from our warehouse in Burton on Trent).
We are now looking to find ways to introduce our ecommerce and wholesale customers to Polyloop – for now we keep the bags on their deliveries for extra protection in transit.
3. 30% recycled content is a start – our ambition is to get to 100% (fully closed loop recycled, and recyclable)
To achieve 100%, we need to find ways of increasing the number of bags fed into the closed loop system.
Superdry was one of the first brands to start working with Mainetti, we have sent more than 2.5 million bags to Wrexham so far. We aim to increase this to over 6 million bags in 2021 but need more brands to join the Polyloop initiative to scale the number of polybags recycled.
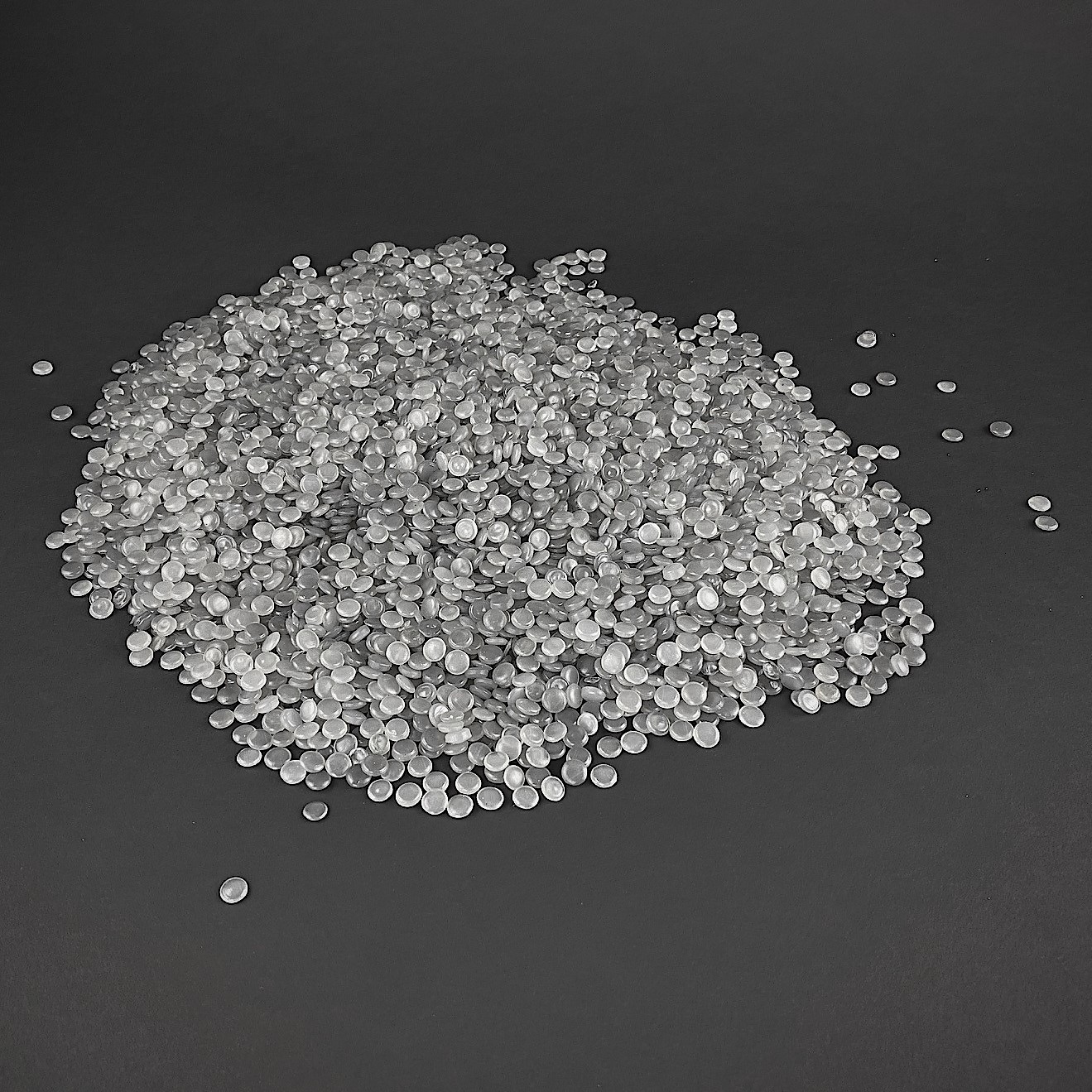
According to a Mainetti study, producing a 100% recycled LDPE polybag emits 63% less CO2e than producing a 100% virgin LDPE polybag.
By increasing recycled content there is a risk the polybag becomes less clear and thicker - recycled plastics often contain prints and other contaminants which impacts the colour and quality of the final product.
PolyLoop will help us combat quality, clarity, carbon emissions and waste.
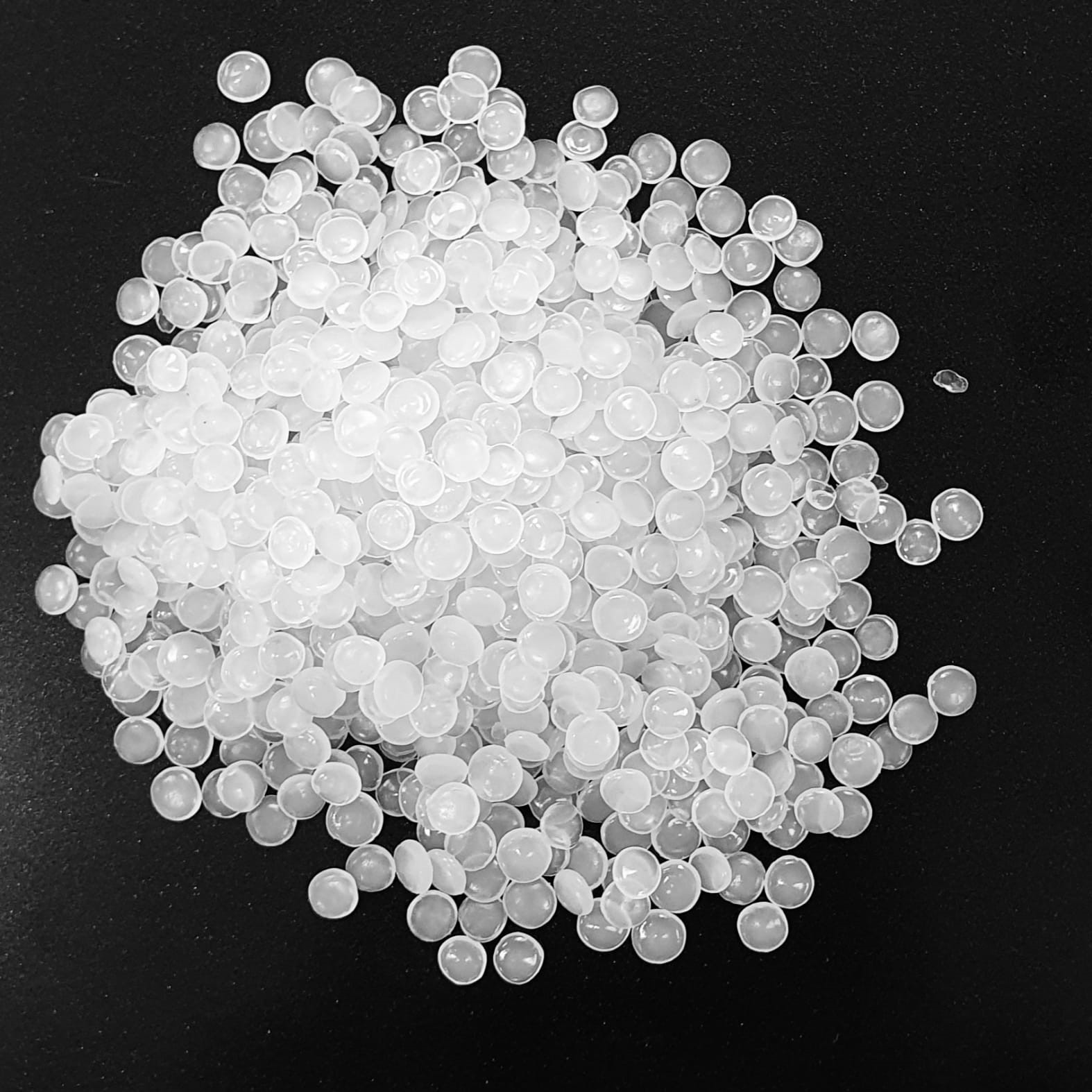
As ever, we will keep you updated with our progress.
If you work for a business interested in joining polyloop please GET IN TOUCH with ourselves or Mainetti.
*https://www.nationalgeographic.org/article/whopping-91-percent-plastic-isnt-recycled/